38.1. Установки тепловой обработки осадков под давлением
Установки тепловой обработки предназначены для кондиционирования органических осадков сточных вод (сырых или сброженных) перед их механическим обезвоживанием.
Тепловая обработка осадков производится в интервале температур 180—205°С и времени 0,5—2 ч. Значения параметров тепловой обработки устанавливают опытным путем по снижению удельного сопротивления осадков. При отсутствии опытных данных следует принимать максимальные значения параметров. В процессе тепловой обработки происходит разложение (распад) органического вещества твердой фазы осадков (ОВТФ).
Степень распада ОВТФ зависит от исходных свойств осадков и параметров обработки. Для осадков городских и близких к ним по свойствам осадков других сточных вод степень распада при температуре обработки 180—200° С ориентировочно можно принимать по табл. 38. 1.
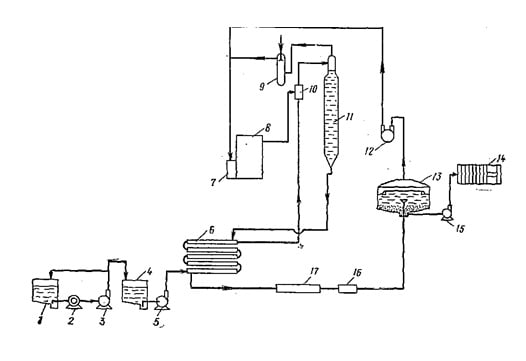
Рис. 38. 1. Технологическая схема тепловой обработки с догревом осадка острым паром
1 — приемный резервуар; 2 — измельчитель; 3 — насос измельченного осадка; 4 — промежуточный резервуар; 5 — насос высокого давления; 6 — теплообменник; 7 — топка; 8 — паровой котел; 9 — сепаратор; 10 — паровой эжектор; 11 — реактор; 12 — вентилятор; 13 — уплотнитель; 14 — фильтр-пресс; 15 — насос для перекачивания уплотненного осадка; 16 — редуцирующее устройство; 17 — холодильник
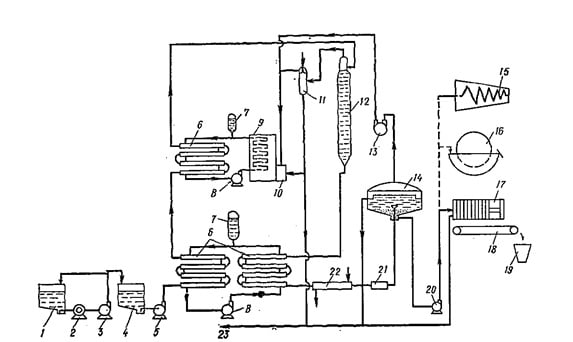
Рис. 38. 2. Технологическая схема тепловой обработки с догревом осадка промежуточным теплоносителем
1 — приемный резервуар; 2 — измельчитель; 3 — насос измельченного осадка; 4 — промежуточный резервуар; 5 — насос высокого давления; 6 — теплообменники; 7 — расширительный сосуд; 8 — насосы промежуточного теплоносителя; 9 — маслонагревательная установка; 10 — топка; 11 — сепаратор; 12 — реактор; 13 — вентилятор; 14 — уплотнитель; 15 — центрифуга; 16 — вакуум-насос; 17 — фильтр-пресс; 18 — конвейер; 19 — бункер осадка; 20 — насос для перекачки уплотненного осадка; 21 — редуцирующее устройство; 22 — холодильник; 23 — отвод воды
Примерно 75—80% распавшегося ОВТФ растворяется в жидкой фазе (иловой воде), а 20—25% переходит в газообразное состояние.
Изменение концентрации ОВ в иловой воде приводит к изменению ХПК и ВПК. Зависимость между этими величинами определяется опытным путем.
Технологические схемы тепловой обработки осадков представлены на рис. 38. 1 и 38. 2. Исходные осадки перед подачей на тепловую обработку необходимо измельчать до получения твердых частиц размером не более 4—5 мм.
При использовании решеток-дробилок РД, обеспечивающих измельчение частиц размером до 8 мм и более, рекомендуется предусматривать многократную (до 3-5 раз) циркуляцию осадков в системе измельчения.
Для подачи осадка в систему тепловой обработки применяются поршневые (плунжерные) или винтовые (червячные) насосы с рабочим давлением до 2,5 МПа.
Нагревание осадка производится в две ступени: сначала в теплообменниках за счет тепла обработанного осадка, выходящего из реактора, а затем за счет внешних источников тепла. Для рекуперации тепла применяются преимущественно теплообменники типа «труба в трубе» по нормалям Министерства химического и нефтяного машиностроения. Теплообмен может осуществляться по схеме «осадок—осадок» (см. рис. 38. 1) или с использованием промежуточного теплоносителя (см. рис. 38.2). Опыт показывает, что при работе теплообменников по первой схеме межтрубное пространство забивается твердыми частицами осадка. В этих случаях применяют разборные теплообменники для загрязненных сред по нормалям ОН 26-02-118-69 и ОН 26-02-119-69.
При работе теплообменников по второй схеме исходный и обработанный осадок подают по центральным трубам самостоятельных групп теплообменников, а по межтрубному пространству циркулирует в качестве промежуточного теплоносителя умягченная вода.
При использовании промежуточного теплоносителя применяют неразборные теплообменники, проектируемые по нормалям ОН 26-02-152-69 и ОН 26-02-153-69.
Для всех теплообменников минимальный диаметр внутренней и наружной труб следует принимать равным соответственно 80 и 125 мм. Трубы, соприкасающиеся с осадком, изготовляются из нержавеющей стали, а соприкасающиеся с промежуточным теплоносителем, из обычной стали. Теплообменники рекомендуется помещать в закрытый теплоизолированный бокс, что позволяет исключить необходимость устройства теплоизоляции на каждой трубе теплообменников. Бокс можно размещать в производственном корпусе или на открытой площадке, следует предусмотреть возможность промывки теплообменников от накипи и других отложений. Промывка производится 10%-ным раствором ингибированной соляной кислоты. Температура осадка на выходе из теплообменников на 35—40° С ниже требуемой для обработки. Догрев осадка, выходящего из теплообменников, до заданной температуры может осуществляться несколькими способами. Наиболее простым и высокоэффективным способом является нагрев острым паром (см. рис. 38.1), который через эжектор вводится в подающий трубопровод осадка перед реактором. Преимущество этого метода состоит в возможности использования пара сравнительно низкого давления с температурой, приближающейся к температуре обработки осадка, т.е. к 190—210° С; недостатком способа является потеря конденсата. Расход пара определяется технологическим расчетом. Для ориентировочных расчетов удельный расход острого пара можно принимать 100—120 кг на 1 м3 обрабатываемого осадка.
Догрев осадка может производиться также в отдельной группе теплообменников высококипящими органическими теплоносителями (ВОТ), поступающими от специальных нагревательных установок (см. рис. 38. 2). Теплообменники этой группы имеют такую же конструкцию, как теплообменники первой ступени, и помещаются вместе с ними в один бокс.
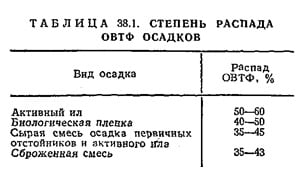
Реакторы для тепловой обработки выполняются в виде вертикальных колонн. При этом следует стремиться к возможно меньшему отношению диаметра реактора к его высоте. Под колпаком реактора оставляется свободное пространство для выделения парогазовой смеси, которую периодически стравливают. Стравливаемая из реактора смесь состоит из водяного пара и газообразных продуктов распада ОВТФ осадков и обладает специфическим неприятным запахом. Для дезодорации смесь направляют в сепаратор, где она промывается очищенной водой. Промытые и охлажденные газы отсасываются из сепаратора вентилятором и подаются на сжигание в топку котлов или маслонагревательных установок. Масса пара, стравливаемого со смесью, составляет 2—3% массы осадка, подаваемого в реактор. Из реакторов осадок поступает в теплообменники под давлением собственных насыщенных паров, которое составляет 1, 8— 2, 2 МПа. Подача осадка в реактор осуществляется постоянно, а выгрузка — периодически через специальные редуцирующие устройства (клапаны, диафрагмы, шлюзовые камеры), установленные на выходящем трубопроводе осадка перед уплотнителем. Выгрузка осадка из реактора производится по положению уровня, контролируемого радиоизотопными датчиками. Осадки уплотняются в уплотнителях радиального типа, снабженных скребковым устройством. Продолжительность уплотнения может колебаться от 1, 5 до 8—10 ч. Влажность уплотненных осадков 93—95%.
Вследствие испарения воды с поверхности уплотнителей в атмосферу выделяются неприятные запахи. Для уменьшения степени испарения осадок, выходящий из теплообменников, дополнительно охлаждают в холодильнике до температуры 30—35° С. Кроме того, над уплотнителем устраивается легкое перекрытие с организованным отсосом воздуха. Уплотненный осадок откачивается плунжерными насосами и подается на механическое обезвоживание.
Механическое обезвоживание осадков после тепловой обработки осуществляется преимущественно на фильтр-прессах; реже применяются барабанные вакуум-фильтры и еще реже — центрифуги. Предпочтительнее применять фильтр-прессы. Они обеспечивают получение осадков с наиболее низкой влажностью — до 45—50%, что особенно важно при последующем сжигании осадков. Для обезвоживания на вакуум-фильтрах и в центрифугах температура обработки осадка в реакторе должна быть на 10—15° С выше, чем при обезвоживании на фильтр-прессах. Влажность обезвоженных осадков можно принимать; для вакуум-фильтров — 68—72%, для фильтр-прессов — 45—50%, для центрифуг — 73—78 %. Производительность обезвоживающих аппаратов устанавливается опытным путем. Для ориентировочных расчетов можно принять производительность: барабанных вакуум-фильтров — 10—12 кг/(м2*ч), фильтр-прессов типа ФПАКМ —12—15 кг/ (м2*ч).
Очистка иловой воды, отделенной в уплотнителях и обезвоживающих аппаратах, осуществляется биологическим путем в аэробных и анаэробных условиях, а также физико-химическими методами. Наиболее распространенной является очистка иловой воды в аэротенках. Применяется совместная очистка иловой воды с поступающими стоками либо локальная очистка на высоконагружаемых аэротенках. При этом дополнительную нагрузку на аэрационные сооружения по БПК5 ориентировочно можно принимать: для иловой воды после тепловой обработки избыточного активного ила — 11—13%; смеси осадка первичных отстойников и активного ила — 22—25%; сброженной смеси — 16—18%. За рубежом применяют сбраживание иловой воды в метантенках. В особых случаях, например при замкнутых системах водопользования, иловую воду подвергают выпариванию.